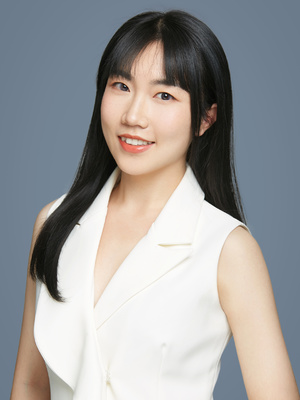
Laura Zhang
Sales & Marketing,HJT EXPO
Phone | +86 10 58677126 |
---|---|
Fax | +86 10 58677126 |
wenting.zhang@interfoam.cn | |
Address | Rm 2003, Building A,Timecourt, Chaoyang District, Beijing, China |
If high stiffness and low weight are key requirements for industrial manufacturing and component design, then rigid foam core materials are the best candidate. Foam core materials are widely applied in sandwich-structured composite materials with its unique properties, showing robust "hard core" strength in such industries as green building, automobile, aerospace, marine, wind energy, and sports, thus laying a solid foundation of high-performance materials for the development of the national economy.
As one of the most common core materials, rigid foams are the ideal choice for manufacturing various types of boards, including flat (or free), lightweight and rigid ones. All kinds of foam core materials can provide additional desired features to final products, such as cost-efficiency, low water absorption, good sound and thermal insulation, FST resistance or insulation. They are components with a very high stiffness-to-weight ratio and a high flexural strength-to-weight ratio. In particular, the boards made of lightweight, high-density structural foam core materials have higher compressive strength and crush resistance than those made of ordinary non-structural foam core materials.
The polymer foams used to produce core materials are made of diversified rigid expansion materials, also known as rigid foams, including the expansion materials, foam metal structures and other composite structural materials of polyurethane (PU), polyvinyl chloride (PVC), extruded polystyrene (XPS), polymethacrylimide (PMI), polyetherimide (PEI), polyethylene terephthalate (PET), styrene acrylonitrile (SAN), polyethersulfone (PES), polyimide (PI).
Foam core materials are widely used in the manufacture of sporting goods, such as windsurfing board, kiteboards, wakeboards, snowboards, racing parts, beach rackets, etc.
The requirement for high quality and low cost of product lifespan has turned manufacturers' attention to structural foam core materials. Composites with rigid foam core materials can help manufacturers reduce fuel consumption and increase payload. Aircraft interiors, cabin side walls, trunks, head and galley access, crew rest areas, bulkheads and seat shells are commonly made from high-stiffness foams.
Sandwich composites with foam cores support better light-weight structure design, and its development is driven by less fuel consumption, higher payloads and a positive impact on the environment. Structural foam cores are used in structural components such as floors for high-speed train and automobiles, body side protection strips, instrument panels and armrests. Structural foam cores of special flame retardant grade are commonly used in private vehicles and public transportation as they can prevent fire, smoke and toxicity.
Weight, quality, cost and impacts on the environment are crucial factors when building a small boat or luxury yacht. Rigid foam cores are lightweight materials, having excellent mechanical property, consistency and moisture resistance. Therefore, they are commonly seen in marine applications, especially hulls, bulkheads, decks, hatches, interior parts such as floors and walls.
Every application on the sea floor requires high-performance equipment for safety as it is a very challenging environment. Structural foam cores are suitable for its high strength, low weight and excellent buoyancy.
Light weight, high strength, energy efficiency, flexible design, and durability are the greatest advantages of rigid foams in the manufacture of antennas, radomes, and antenna tower structures in radar and telecommunication industries.
The requirement for durable and heavier turbine blades has driven manufacturers to use core materials, primarily high-performance structural foam cores, which can produce larger, stronger, stiffer, but more lightweight blades. Thus, structural foam cores will help reduce costs and increase the efficiency of wind power plants.
——————————————————————————————————————————————————
Interfoam China is a professional exhibition for the whole foam industrial chain in Asia, and is an international event that cannot be missed by the professionals from foam industry all around the world.
Interfoam China focuses on the latest production, technology & equipment, new techniques, new trend, and new application in foam industry, and spare no effort to provide a professional platform integrating technologies, trade, brand display, and academic exchanges for its upstream and downstream as well as vertical application industries, thus promoting industrial sustainability.
Sales & Marketing,HJT EXPO
Phone | +86 10 58677126 |
---|---|
Fax | +86 10 58677126 |
wenting.zhang@interfoam.cn | |
Address | Rm 2003, Building A,Timecourt, Chaoyang District, Beijing, China |
Industry news
Dow (NYSE: DOW) will showcase the breadth of its materials science solutions to demonstrate how plastics can power positive change and a more sustainable, customer-centric future under the theme “Generation Transformation” at K 2025 in Dusseldorf, Germany.
Industry news
BASF has signed a Memorandum of Understanding (MoU) with Shanghai Fourier Intelligent Technology Co., Ltd. (Fourier) to evaluate and develop new material solutions for various robot applications.
Industry news
Essen, Germany. Evonik is making further strides in its sustainability journey with the conversion of its remaining PU-additive production assets across the globe to green electricity. The entire Comfort & Insulation business line’s global polyurethane (PU) production footprint now runs on green electricity.
Industry news
Recently, Interfoam and Foam Update (led by Dr. Shau Tarng Lee) reached a cooperation agreement. Based on their two-year-cooperation from 2023 to 2024, both parties have decided to hold the 9th PFC2025 Polymer Foam Conference in Suzhou in November 2025.
Industry news
On June 27th, Yaël Braun-Pivet, President of the French National Assembly, leading a high-level delegation, visited SGRS and Sekurit production site in Minhang District, Shanghai.
Industry news
Interfoam, as the leading foam industry exhibition in Asia, collaborates with senior partners in the polyurethane industry to create the "Polyurethane Foam Special Exhibition" during the 4th Interfoam Exhibition. The special exhibition aims to promote the application and development of polyurethane foam materials in different fields, and help upstream and downstream enterprises of polyurethane foam obtain new orders and develop new markets.
Industry news
There is an increasing demand worldwide for more and better packaging solutions. As well as improved performance, businesses and end consumers are prioritizing sustainability, driven by individual and corporate commitments and, increasingly, by legislation. Carpenter is at the forefront of these trends, offering customized packaging solutions that protect and cushion products while reducing the environmental impact of manufacturing and logistics.
Industry news
Mega Master Technology Co., Ltd. is a high-tech enterprise specializing in the research, development, production, and sales of polyolefin foam. The company is headquartered in New Taipei City, Taiwan. Mega Master Technology's main products include irradiated cross-linked polyethylene (IXPE), irradiated cross-linked polypropylene (IXPP), and other high-performance electronic materials, which are widely used in the electronics, automotive, and construction industries.
Industry news
Zotefoams - a world leader in supercritical foams–is making its debut at The Battery Show Europe at Messe Stuttgart, Germany where it will be showcasing its high purity and lightweight materials for various applications in battery packs.
Founded in 2011, HJTEXPO is a leading trade show organizer specialized in curating niche-focused exhibitions and conferences. Centered on three core pillars—Knowledge, Technology, and Business, we are dedicated to crafting a professional service ecosystem that empowers clients through offline face-to-face interactions, enabling high-value business transactions.
Please browse vertically for better experience.